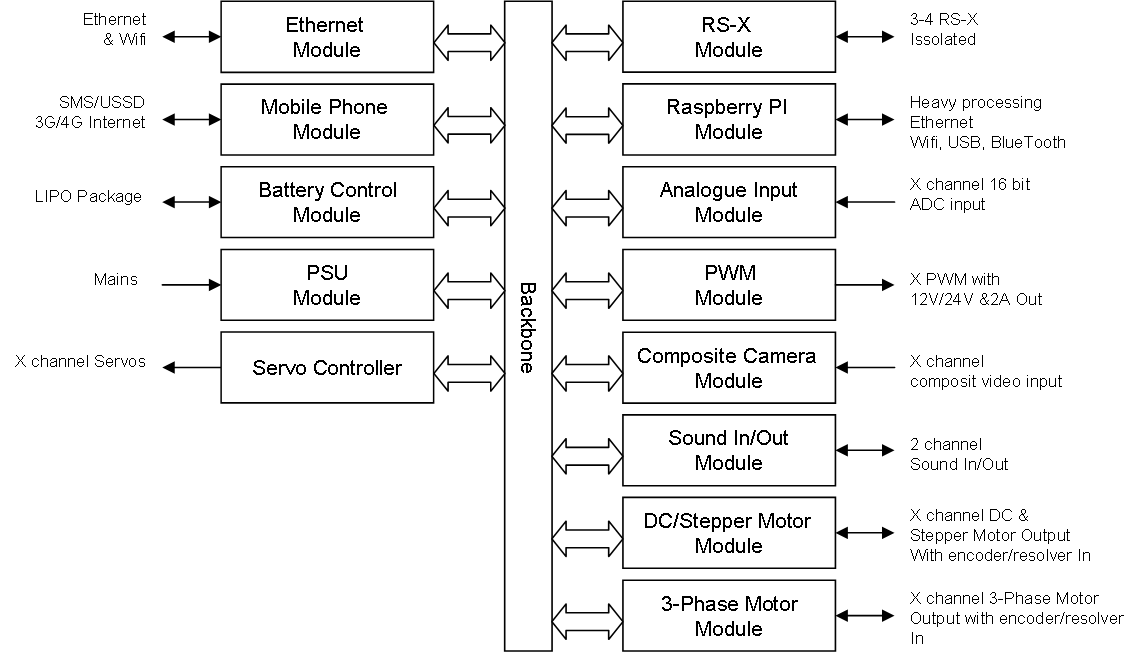
Using STM32F405RG on everything is an overkill, but I can always consider dropping down to STM32F105RB/C later. This M4 gives us a powerfully MCU on each module capable of truly distributed processing as we are promoting in Plain.
Ethernet Module is what I have started on now. This will host a STM32F405RG, 2 RS-485’s for the backbone, a W5500 based Ethernet and optionally a ESP-12 module for wireless. I am also adding RTC battery, SPI flash and a SWD connector. I need to see what space I have available, but as with my previous Raspberry PI Hat’s I intend to re-use much of the MCU related design on every Board if pins & space allow it.
RS-X Module connect the 2 backbone lines to 3-4 isolated network lines. I want isolation on anything in & out of the PLC.
Mobile Phone module is for internet connectivity on remote places or as a secondary backup should a primary internet be cut. It exist so many small, low cost modules these days that we just grab one of those.
Battery Control Module is so we can connect a LIPO package to operate if mains fall out. This should also include charging and monitoring of the battery.
PSU Mains Module is basically PSU modules needed for 5V, 12V, 24V &48V.
Raspberry PI Module will allow us to interconnect with a Raspberry PI for computing, Ethernet, Wifi, USB, Bluetooth etc. The target here is Raspberry PI 2, 3 or Zero W.
Analogue Input Module is a x channel 16 or 24 bit ADC input module. This allow us to read analogue sensors with some accuracy. We need more than the internal 12 bit ADC, so I am thinking maybe a low cost 12 bit board and a bit more expensive 24bit board.
PWM Module is a x channel PWM output, each channel formed as a Half H-Bridge and supporting 2A continuous current. We probably should manage 8 channels – not shure.
Composite Camera Module. I am not sure about this board as I am tempted to use H.264 camera’s only in which case I will ditch this module.
Sound In/Out Module is basically targeting doorbell, but I am open for the possibility to provide a multi-channel music mixer as well. I need to consult with friends in the London music industry a bit, and it is possible this actually will be several boards to adapt to a stage show.
DC/Stepper Module will basically be very similar to the PWM module, but I probably need various currents & voltages for different motors. I am thinking only of small motors supported directly because I expect separate controllers for the larger motors.
3-Phase Motor controller – well, the name say it all, but I am not sure I want to make this board. The reason is because a 3-phase motor usually require some power that is better handled on a separate controller on the other side of an isolated RS-X. Let’s see…
Servo Controller is probably a 16 channel controller like we created before on a Hat, but I will be using Timer’s for PWM this time to get a 16-bit resolution on the PWM duty out.
As mentioned a few times before – this is an idea draft and I write it down to let it mature – plans will change.