I have just made both these boards, but strugled far more to route the PWM3 board than Ethernet board – looking at the two I got a bit surpriced – On the top board (Ethernet) you can see the same infrastructure components as on the bottom outlined – the top has an extra SPX3819 and SPI-Flash, but notice the difference in density – how much space they occupy. I will order these regardless, but I do notice that on top layer I use ca 60% for MCU and on bottom layer ca 30% for standard ecostructure. Basically I have marginal space for IO as is.
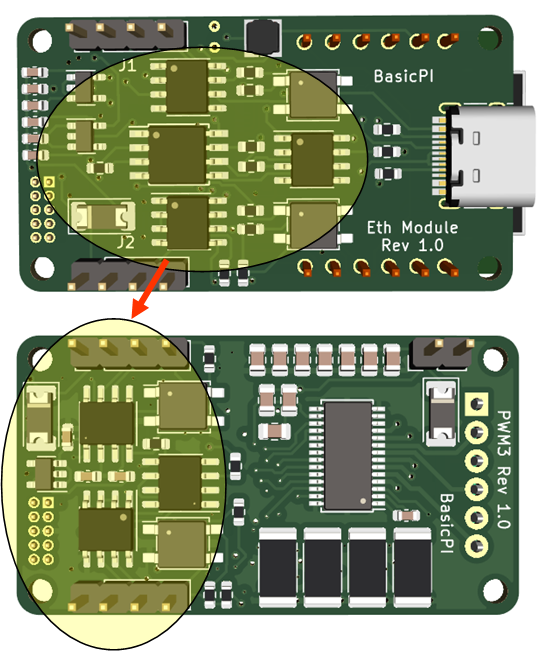
But, keep in mind that this design allows for larger modules – double height and double width as well. It does however question how many of my modules that I can do as 25 x 45 mm size. It also make me consider increasing the minimum module size – that said I am as hesitating to increase as I was to decrease size – I want to give it a try first – collect experience. There will guaranteed be a revision 1.1 of these boards anyway.
One concern is that the W5500 breakout pins get to close to 24V power pin – I will leave that as is, but it might need attention later.
A bigger concern is the need for 24V, 12V and 5V for IO. I have som 60Kg servoes and would like to connect them as well – they need 5 or 12V – so what I am thinking is to extend the 2 pin header with GND, 24V to a 4 pin with GND, 24,12 and 5V – you simply only provide the pins you use. The header pins are good for ca 10A and the PSU is not the modules problem here (motherboard or extern module).
For now I will just add a simple 5V PSU for MCU on the motherboard and use an external PSU as power driver, but I will need all 4 layers to deliever power here because motors and servoes are suckers to power up – servos have a tendency to start and align a position as you power up – and for 12 small servoes I needed ca 10A in peak. Power usage once started is smaller and can be controlled in software.
I am thinking two different servo modules – one for 2x power servoes, and one 6 channel. I might also make a double width module with 16 channels etc – lets see.
Servo and/or Distance TOF interface is my next module(s). The TOF is needed for robotics being able to sence their surroundings and I will start with my own car because I lack distance censors in back and front.